“Tag, you’re it!”—that saying always makes me laugh. From childhood to adulthood, when you get “tagged” with a task, it’s all on you! So, when a customer contacts you to come to their space to figure out what’s wrong with their resilient flooring, it’s all on you to provide them with some answers to their concerns.
Understanding Resilient Flooring Types
Resilient flooring, covering about 28% of the commercial market according to Floor Focus magazine, offers durability, a vast array of styles, and relative ease of maintenance. However, even the most durable resilient floor can succumb to cleaning woes if not cared for properly. This article will guide you through inspecting resilient flooring for cleaning issues, helping you maintain its appearance and functionality.
Before assessing the issues, it’s crucial to understand the various types of resilient flooring, as each has unique cleaning and maintenance requirements.
Luxury Vinyl Tile (LVT) & Luxury Vinyl Plank (LVP): An extremely popular choice for the last 15 yrs. LVT/LVP offers realistic wood, stone or frankly any material you can imagine at a lower cost than the real thing.
LVT flooring is made up of multiple layers:
- A factory applied urethane coating (sprayed on)
- A clear wear layer that protects the design from scratches, stains, and fading.
- A design layer (photograph) that creates the realistic look of wood, stone, or other materials.
- A core layer that provides stability and comfort underfoot.
- A backing layer that is adhered to the subfloor.
Sheet Vinyl Homogeneous (HO) or Heterogeneous (HE): These come in rolls and are perfect for large, open spaces likes medical facilities. Sheet vinyl is known for its water resistance and can be heat or chemical welded to make it a liquid barrier and easy cleaning, making it ideal for areas prone to spills. HE Sheet Vinyl is made up of multiple layers and HO Sheet Vinyl is the same throughout.
- Both types come with a factory applied urethane coating (sprayed on)
- HE comes with a clear wear layer that protects the design from scratches, stains, and fading.
- HE has a design layer (photograph) that creates the realistic look of wood, stone, or other materials.
- A backing layer that helps to prevent moisture from damaging the subfloor.
Vinyl Composition Tile (VCT): VCT is known for its affordability and long-lasting performance. Vinyl composition tile is a resilient tile floor covering composed of binder, fillers, and pigments compounded with suitable stabilizers and processing aids. The binder consists of polymers and copolymers of vinyl chloride, other modifying resins, and plasticizers Due to its construction, VCT is porous, and requires an acrylic floor finish. VCT is also fairly brittle (when not glued to a substrate), so it only comes in 12” x 12”. It’s available in a vast array of colors.
Vinyl Enhanced Tile (VET): Technically vinyl enhanced tile is vinyl composition tile; the primary difference is that it contains more binder and durability, and it comes with a factory applied urethane (sprayed) coating, which can reduce the maintenance cost.
Solid Vinyl Tile (SVT): Solid vinyl is a floor covering composed of binder, fillers, and pigments compounded with suitable stabilizers and processing aids. The binder consists of polymers and copolymers of vinyl chloride, other modifying resins, and plasticizers, which comprise at least 34% of the weight of the finished tile. SVT comes with a factory applied (sprayed) urethane coating. Because of its vinyl content, SVT can be made in much large sizes, offering many more design choices.
Woven Vinyl: A newer product to the market in the last ten years but has grown in popularity in the design community. A similar product to LVT in its backing construction, it varies however in how the design on the surface is displayed. This presents a challenge for maintenance professionals as soil can be trapped in the weave on the surface of the product.
Rubber Flooring: Rubber Flooring – Styrene-butadiene rubber (SBR) can come in Homogeneous (HO), Heterogeneous (HE), and Bonded Rubber Crumb (recycled) sheets or tiles. Rubber floor coverings are extremely dense, durable, and slip-resistant products used extensively in many different environments. Due to its versatility, it’s used in hospitals and schools, along with corporate and industrial environments.
Note: Rubber is a pH sensitive material and any chemistry used should be below 10.5 on the pH scale.
- SBR HO is sometimes identified by having small or large, pronounced raised squares or rounds on the surface, but can also be smooth or textured, solid in color, or a kaleidoscope of colors, and they are available in rolls and tiles.
- BRC (Recycled) – Offering excellent slip resistance and sound absorption.
Cork Flooring: Cork flooring is made from the bark of the cork oak tree. Cork flooring comes in basically two variations, solid or engineered. Most all cork flooring comes with either a factory applied urethane coating or comes raw, however both styles receive an onsite urethane coating is applied after installation. Cork is extremely absorbent, so maintenance should be done with a focus on using as little water as possible. Sustainable and naturally comfortable underfoot, cork flooring provides a touch of luxury.
Linoleum: One of the oldest floor coverings currently available, linoleum, is an all-natural floor covering. It is a resilient floor covering composed of a solidified mixture of linseed oil, pine rosin, fossil or other resins or rosins, or an equivalent oxidized oleo-resinous binder, ground cork, wood flour, mineral fillers, and pigments bonded to a fibrous or other suitable backing. Linoleum also has a factory applied urethane (sprayed) coating as a protective layer. Linoleum comes in many color options and can come in tile and roll (sheet). Because of its flexibility and ease of work, this decorative floor covering is often cut and lain in artistic motifs and produces some wonderful-looking floors.
Note: linoleum is a pH sensitive material and any chemistry used should be below 10.5 on the pH scale.
Electro-Static Discharge Flooring (ESD, but can also be listed as Static Dissipative Tile or SDT): One of the more unique products within the resilient market and has a very specific installation environment. Usually found in computer server rooms, clean rooms, and manufacturing spaces where materials used are sensitive to electrical charge. These products are more commonly found as a vinyl product but can be manufactured as a rubber material. These flooring materials will have very specific maintenance requirements, including special cleaning chemistries and special floor finishes, as inhibiting the ESD properties of this material can be disastrous for the owner of the space, and ultimately the maintenance provider.
Inspection Considerations Based on Building Environment
The environment of a facility represents all the conditions and influences that affect the habitat and cleanliness of the building. The environment helps to identify the types of soil introduced into the facility, whether they are natural (cellulose, sands, and silicas) or manufactured (oils, chemicals).
The geographical location and weather have a major impact on the environment of most facilities. Dry, arid regions tend to have more sand. Wet, rainy regions are harsher for floor coverings because of the combination of moisture and soil. Areas that are subject to snow have special problems; the chemicals required to keep sidewalks from icing are very hard on floor coverings and coatings.
Parking lots and sidewalks contribute to external soil that comes in from outside and create environmental issues inside. Tar, asphalt, and sealants that track into a facility (petroleum migration) create huge issues.
In addition, there are types of soil generated within the facility by the mechanical apparatuses that facilitate HVAC, elevators, and other systems. This soil is different from the outside soil, but they also affect the building’s environment. A major contributor to soiling is the classification of business that occupies the facility and the kind of services or products they manufacture or sell. The business environment classifications help us to identify the types of soil that will most likely be present. Soil identification is critical for chemical selection.
Commercial properties are general office buildings located in most metropolitan areas, such as insurance, banking, legal, and large or small corporate enterprises. There are generally three classifications of commercial environments: “Class A,” “Class B,” and “Class C.” These classifications can impact the flooring because of soil conditions, but more importantly because of the level of cleanliness expected.
- Class A commercial facilities are the most prestigious buildings competing for premier office users with rents above average for the area. Buildings have high-quality standard finishes, state-of-the-art systems, exceptional accessibility, and a definite market presence.
- Class B commercial facilities are competing for a wide range of users with rents in the average range for the area. Building finishes are fair to good for the area, and systems are adequate, but the building does not compete with “Class A” facilities at the same price.
- Class C commercial facilities are competing for tenants requiring functional space at rents below average for the area. The level of cleanliness in these types of facilities is generally basic or below.
Questions to Consider
- What type of dissatisfaction is in question? Scratching, staining/discoloration, hazy/dull appearance, slippery, gapping/peaking, cloudy, sticky, or soiling?
- Where is the flooring of concern located? Lobby, first floor, elevator lobby, higher floors, restrooms, back of house, general or specific high-traffic areas, or kitchen areas? Is it isolated to one area or multiple?
- Do you know who the manufacturer of the flooring is, and when was it installed? Refer to the manufacturer’s cleaning guidelines for specific instructions on cleaning products and techniques (this information can be found on their website).
Inspection Process
Visual Inspection: Start by looking for cleaning-related issues like:
- Is the outside of the entrance dirtier when leaving the space than coming towards it? See Image 1.
- How close are you to any asphalt-covered surfaces?
- Does it appear that any of the surfaces leading up to the building were just recently repaired or replaced?
- Is there walk-off matting present? If so, what kind of walk-off matting? The vestibule in Image 2 may as well be just hard surface.
- How is it being maintained?
- Does it need to be replaced?
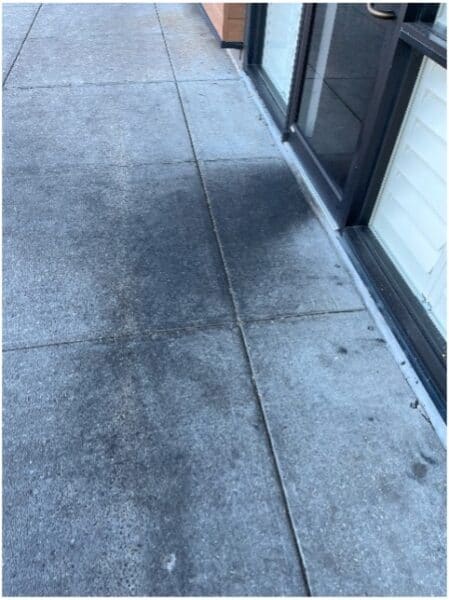
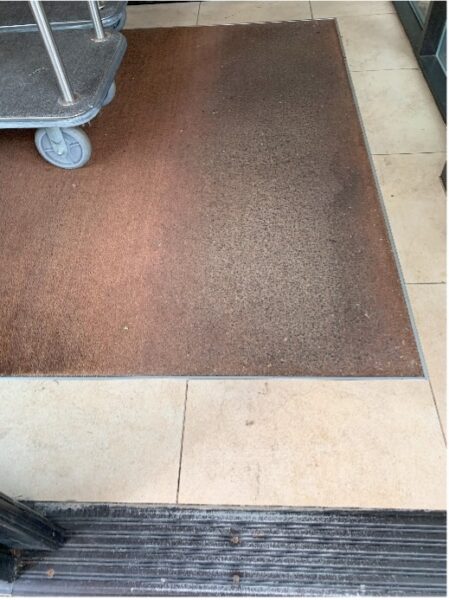
Absolutely the number one question I’m asked is, “Can you tell me why my new floor has scratches or scuffs?”
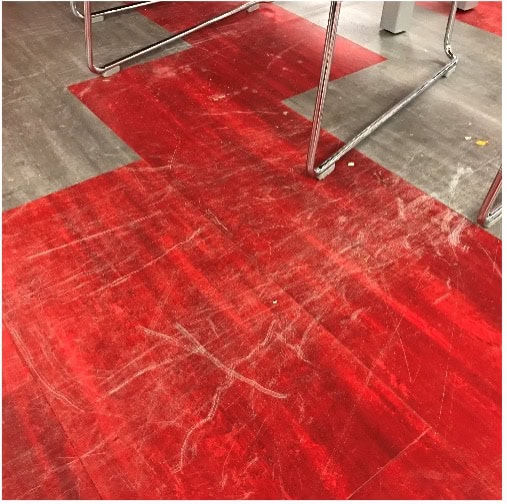
In the design and purchase processes, words like “low maintenance” are often used when describing resilient flooring. “Low” gets confused with “no” in a lot of cases, and since there isn’t really magic fairy dust available to make the soil disappear, we need to educate the customer on what needs to be done. Now, that’s not saying the material is not engineered/designed properly. The customer should be doing dry soil removal (dust mop or vacuuming with suction only) every day, and a good walk-off system should be in place and maintained properly.
As we talked about in the materials section, almost all the flooring types come with a factory-applied urethane coating, and the heterogeneous materials have a clear wear layer to protect the image. A common issue on the ground floor is excessive abrasion caused by soil (sands and silicas) not being trapped in the walk-off system, making their way under the soles of shoes and causing abrasion and scratches on the surface of the flooring. These can be less noticeable on patterned and textured flooring options.
When a walk-off system is “non-existent” and dry particulate isn’t done, excess wear can happen quickly.
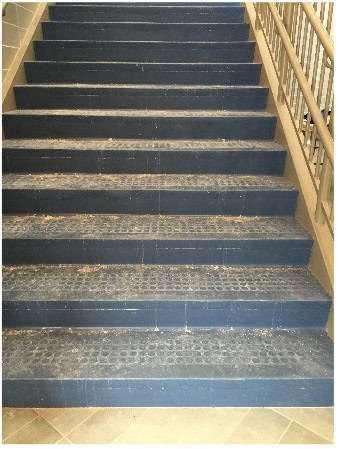
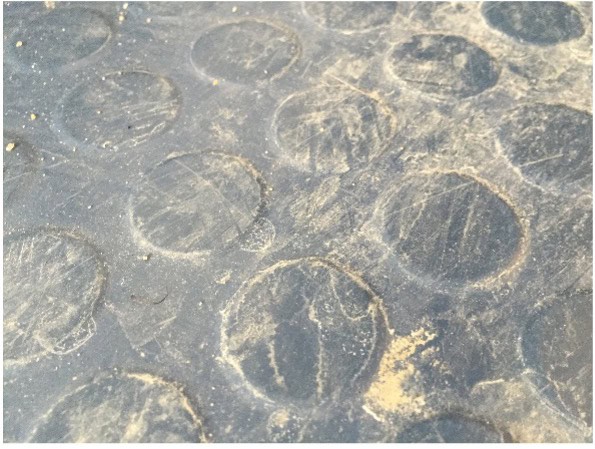
Moh’s Scale
Let’s look at what can scratch resilient floors. Most plastics (acrylics, urethanes, vinyl, etc.) reside somewhere around a 2.5 on the Moh’s scale of hardness. Sand/silica is around a 7. It’s much harder and will win the battle every time. The common response that we see is, “There is _____ additive in this coating, so it is harder and won’t get damaged” (could be aluminum oxide, ceramic bead, or even diamond dust). Remember, that additive is still mixed in with the plastic coating and will still be around 2.5 on the Moh’s scale.
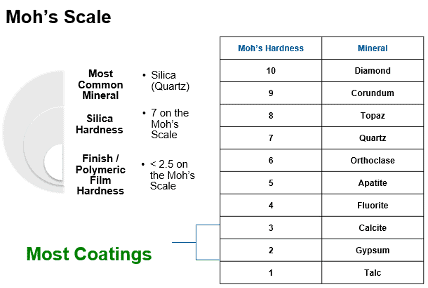
Wear vs. Damage
I often start at the doorway of the space in question; if everyone is coming in and out at that point, then if excess wear is an issue, it should be most visible at that point. If the flooring looks “ok” there, then more often than not, issues inside the space are caused by damage and not wear.
Staining & Discoloration
Another issue, although not as prevalent, is staining/discoloration:
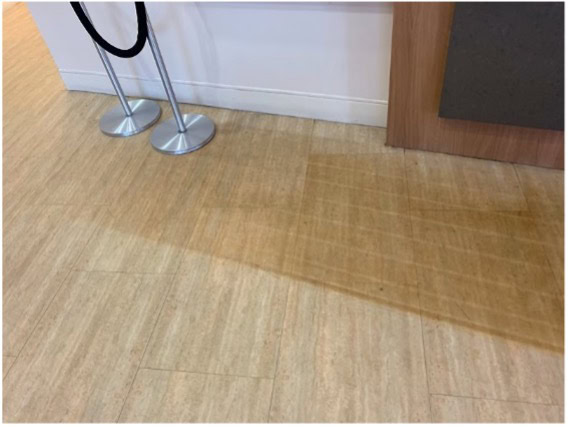
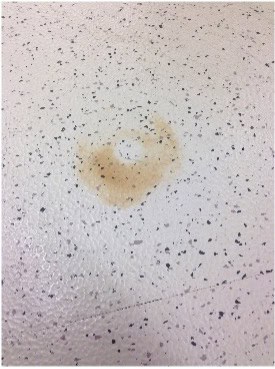
- Staining or discoloration can be hard to identify. Is it topical, or is it a subfloor issue? If there is either a factory-applied urethane and a wear layer on the flooring material, chances are any visible stain will not come out.
- Sometimes it’s materials that don’t play nice together, like rubber and vinyl.
- Excessive use of disinfectants without rinsing can discolor materials. In this photo, a piece of attic stock (rubber) was installed to show the staining that has occurred over a period of time. [Image 9]
- Lobby and first floor: Issues such as asphalt “walk-off” caused by oils tracked in the building are left on the flooring and oxidize, leaving a yellow appearance. I have also seen discoloration caused by improper use of cleaning products with dyes in them (over diluted). [Image 10]
- UV staining: Another form of staining that we see is from UV light, which most of the time is related to sunlight exposure. Once that flooring is exposed to constant or daily UV light, it will shift the color of the material. Unfortunately, this is not something that a maintenance provider can fix. However, it can be prevented to a certain extent with UV protective windows.
- Hazy/dull appearance is a frequent comment I hear regarding resilient flooring. A trip to the janitorial closet will usually result in finding the issue—a vinegar bottle or dirt mop water in a mop bucket with a mop soaking in it. In northern climates from around December to April, ice melt residue will make a floor look very hazy. [Images 11 and 12]
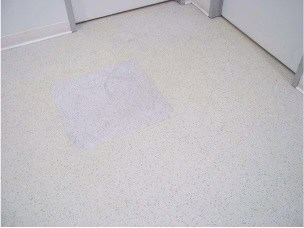
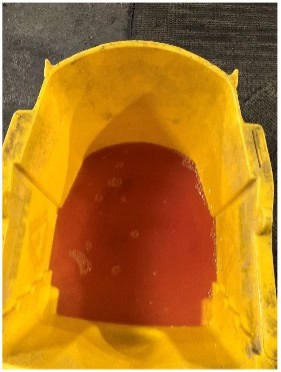
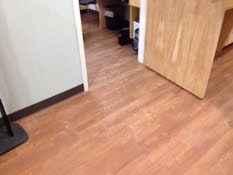
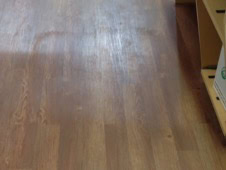
Slip Issues
One very common request I receive is, “My new floor has become slippery.” This can usually be solved easily (see photo, outside is dirtier when leaving) as an improper or nonexistent maintenance program. Sometimes it’s actually the opposite of no maintenance being done. It’s the improper maintenance by either over-diluting the cleaning chemistry, using the wrong chemistry (oil-based), or, most often, not rinsing the cleaning chemistry after cleaning.
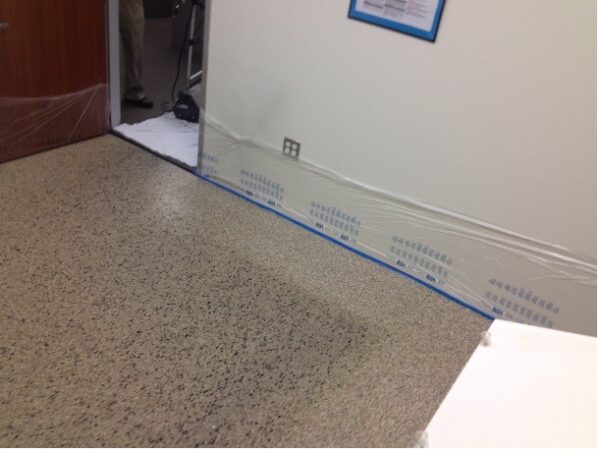
I politely ask the customer, “If you rinse your hair after applying shampoo, or rinse your hands after applying soap, you should think about adding the rinsing step into your cleaning process.” Sometimes it may not be slippery, but if a customer says, “My flooring is dull,” residue from cleaning chemistry not being rinsed can leave a dull film as well. This could also cause the flooring material to be sticky if too much cleaning chemistry is used and not rinsed.
Textured Surfaces Soiling
This is also a common issue. Over the last couple of decades, texture has been introduced in a majority of the resilient sold, and we still try to maintain it with a string mop and a rotary floor pad.
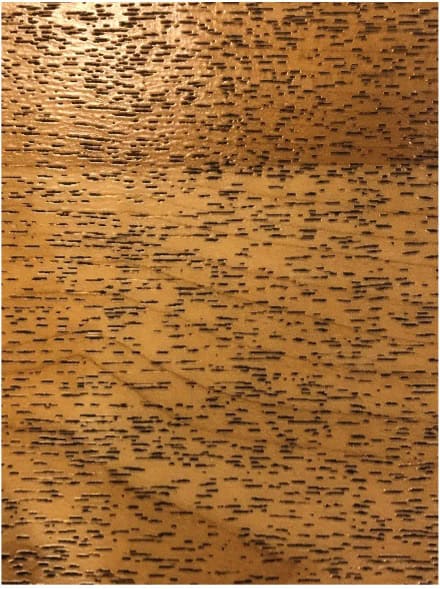
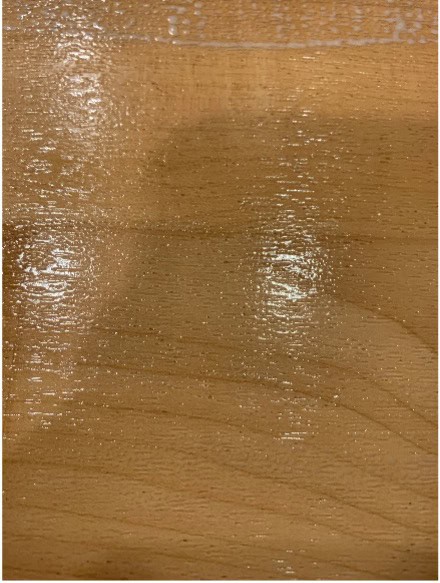
Gapping/Peaking
This is not very common, but it can occur. This can be caused by either one or a combination of events. Most often, a flooring material can gap or peak when it was not properly acclimated to the environment it has been installed in (e.g., it came out of a cold warehouse, into a cold truck, and then was installed immediately in a climate-controlled space). Or it’s installed in an area where the temperature has large swings, such as a vestibule or on a south-facing window wall.
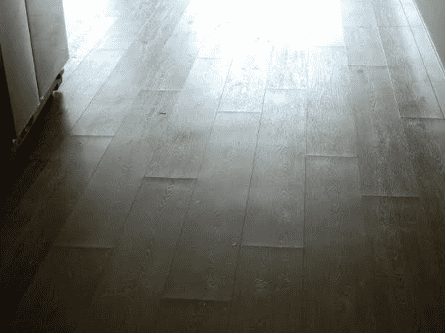
Rectifying Issues
- Slippery or Film Buildup: Try a solution of warm water and agitation. Once in a slurry state, remove and rinse with fresh water.
- Staining: There may be commercially available cleaning products designed for specific stain types on resilient flooring. Test any cleaning solution in an inconspicuous area first.
- Scratches and Scuffs: Minor scratches on some resilient flooring may buff out with a white floor pad, or a maintainer (spray buff) may be applied. For deeper scratches, an acrylic floor finish (such as a matte sheen) can be applied in several coats to “mute” the scratch’s appearance, or a corrective process that includes an on-site application of a urethane coating. Consult a flooring maintenance professional to assess repair options.
- Cleaning and/or Replacing Chair Glides: Consider replacing or cleaning chair glides to prevent further damage.
Prevention Tips
- Develop a Cleaning Routine: Regularly sweep or vacuum to remove loose dirt and debris. Follow up with mopping using the recommended cleaning products and techniques.
- Entrance Mats: Place mats at entry points to trap dirt and moisture before they reach the flooring.
- Spot Cleaning: Address spills promptly using appropriate cleaning solutions.
Conclusion
The key to maintaining resilient flooring lies not only in understanding its diverse types and specific care requirements but also in effectively managing the environmental factors that impact its cleanliness and longevity. By conducting thorough inspections, identifying potential problem areas, and applying targeted cleaning strategies, facility managers can significantly enhance the durability and appearance of their flooring investments. Remember, regular maintenance and proper care are essential to preserving the aesthetic and functional qualities of resilient flooring, ensuring it remains a viable and attractive option for various settings.
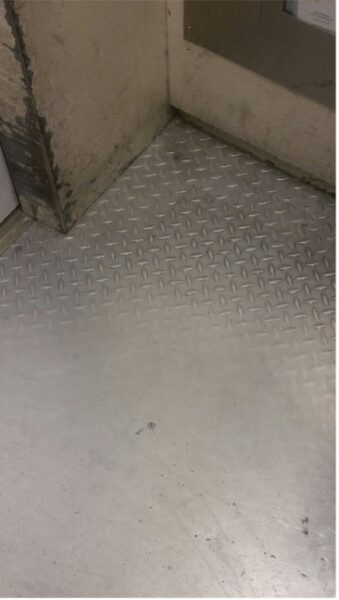
As my dear friend Steve said, “If a metal floor can’t withstand foot traffic, how can we expect resilient flooring to without proper care?”