Written by Rahul Dhavalikar, Director of Product Development, Roppe Holding Company
Is something bothering you with the way the resilient floor appears stained or damaged after installation? Is it costing you valuable time and money? With the increasing popularity of resilient flooring in both commercial and residential settings, there has been a rise in inquiries about issues such as surface abrasion, staining, and discoloration of these types of floors. Surface abrasion is a simple explanation, but understanding the chemical reactions that cause discoloration takes some investigation.
PVC, Rubber, and polyurethane coating on LVT or SPC products are all organic polymers. Organic polymers essentially contain carbon atoms in the backbone whereas the inorganic polymers do not contain carbon atoms in the backbone. Most plastics and rubbery materials are organic polymers. When a chemical reaction occurs, molecular bonds are broken and other bonds are formed to make different molecules. Energy is always required to break a bond, which is known as bond energy. When a bond is strong, there is a higher bond energy because it takes more energy to break a strong bond. The energy to break a bond becomes available from the presence of UV light, heat, and/or strong chemicals capable of attacking a flooring surface.

Resilient flooring products yellow when the polymeric chains degrade. This happens either in the presence of oxygen and UV light (photooxidation) or in the presence of sufficient heat exposure (thermal oxidation). Flooring manufacturers use different technologies to prevent degradation of polymeric surfaces and supply products that meet ASTM specifications. Some of the commonly used technologies are the use of expensive fade resistant polymers, opaque pigments, UV stabilizers, UV absorbers, heat stabilizers, etc. These technologies do not provide permanent resistance to degradation as their potency eventually reduces upon prolonged exposure to heat, UV radiation, or harsh chemicals.
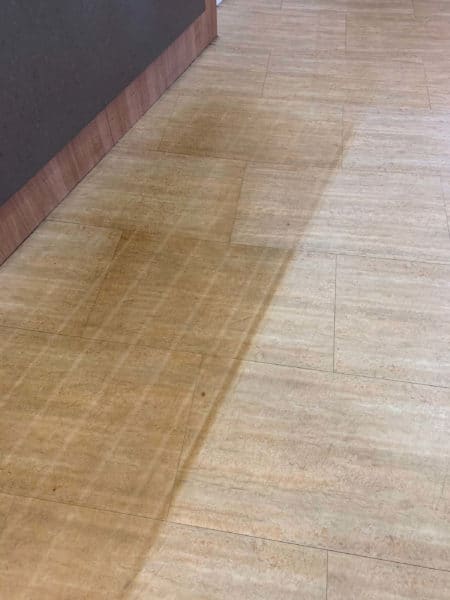
During degradation of polymers in the flooring products, several changes happen in the polymeric chains resulting in yellow color. The color changes from colorless to yellow, brown, and finally to black as the degradation progresses. To prevent undesirable yellowing, it is necessary that manufacturer’s instructions are followed. Most of the resilient flooring are not designed for outdoor installation. Standard specifications such as ASTM F1700 and ASTM F3261 are designed by including performance requirements for resistance to (UV) light, heat, and resistance to chemicals. ASTM standards are consensus-based standards. As the use cases of flooring products are rapidly evolving, it is necessary to keep ASTM standards updated to reflect the challenges faced by existing customers. It is necessary to note that ASTM standards require manufacturers only to test the finished flooring product and not the installed flooring applied with adhesive, cleaning chemicals, and disinfectants.
Many of the resilient flooring products such as LVT, SPC, and Linoleum are sold in the market today by applying a clear wear layer or permanent finish as the top layer in the factory. Resilient flooring manufacturers use proprietary recipes to provide performance attributes to the wear layer. Cleaning products such as heavy-duty degreasers are usually highly alkaline with a pH of 13-14. An acidic floor detergent is often recommended to remove rust stains, mineral deposits, and heavy organic matter. Such acidic detergents range from 2-4 in pH. Both the extremes of acidic and alkalinity of cleaning chemicals permanently stain the surface of resilient flooring products and result in reduced service life of the resilient flooring products. Flooring products with damaged wear layer are prone to scratches and gouges.
During the early days of Covid-19, EPA undertook an initiative to publish List N that provided us the disinfectants that were effective in killing all strains and variants of the coronavirus (Sars-Cov-2) when used according to label instructions. The list N has gone through several updates over the last two years as the new products are being constantly added. Several strong acids and alkaline materials are recommended in the list N that can permanently damage the resilient flooring products if not used appropriately at the correct level of dilution. A conversation with technical experts at the flooring manufacturers and the disinfectant manufacturers is highly recommended prior to use of the disinfectants.
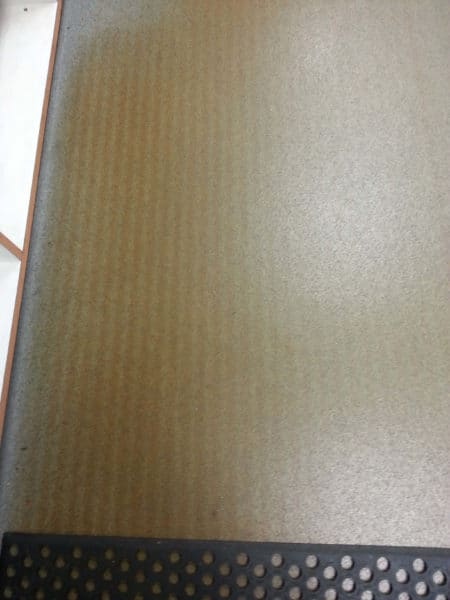
There are certainly other things that can cause staining or oxidation to resilient flooring; oils, tar (asphalt tracking) dispersed dyes like hair coloring, just to name a few. However, Resilient floors can also be subject to staining from migration from below. Hydrostatic pressure from the subfloor can contribute to issues such as mold or mildew, or prior adhesive contamination. When rubber, adhesives, and vinyl flooring surfaces come in contact by design during installation, some of the technologies of plasticizers are known for migration or bleeding to the interface. This has resulted in unpleasant discoloration of the flooring product.
In summary, to prevent staining and discoloration of resilient flooring, it is important to understand the causes and take preventative measures such as using non-staining mats and protective materials, avoiding light-colored flooring, and if needed recommending a removable/repairable floor coating as finish to be the sacrificial surface finish. A quick conversation with technical representatives of a flooring or cleaning chemical or disinfectant manufacturer prior to taking critical steps will go a long way in saving you headaches and dollars over the long run.