The one question I’m most frequently asked (besides the common “how to” industry questions) is, “What can we do or purchase to make us more productive as a floor care company?” so I decided to cut to the chase and provide you with the top 5 tips, in my opinion, that will make things run smoother, produce better outcomes and, yes, make your company more profitable! I also asked industry heavyweights to provide further insight on how these suggestions can positively impact a commercial floor care business’s productivity and efficiency.
In no particular order, they are:
The Fast Foamer
At first glance you might say, “That’s nothing new. It’s a counter rotating brush machine with something else added to it.” That’s where the comparison stops. The company behind the Fast Foamer spent over 20 years evaluating issues in floor care before putting pen to paper to design what is currently the most effective low moisture cleaning system rated by the CRI. With two models available (20 or 40 gallon carts) a technician can clean for an entire shift without ever stopping to refill and when you think about refilling a 2 gallon pump sprayer a minimum of 4 times a night, taking at least 15 minutes to walk there and back and check Twitter, Instagram, and Facebook, you already see savings.
But time is only part of the efficiency package of the Fast Foamer. As water and energy are becoming even more precious, cleaning with the Fast Foamer technology really becomes more evident. I stated that the Fast Foamer is the highest rated low moisture cleaning system by the CRI SOA program, which means it’s up against water rinse extraction equipment such as truck mount and portable extractor systems. The reduced use of water and energy is only part of the equation. It also eliminates the downstream effort needed to reclaim the dirty water.
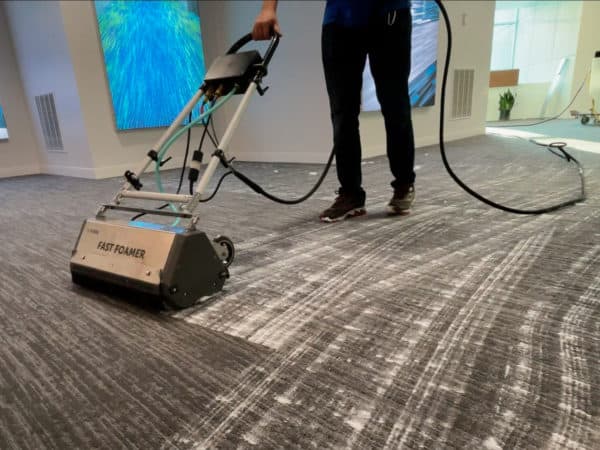
The innovation of the Fast Foamer bridges the gap between interim carpet maintenance and restorative carpet cleaning. It reduces the need for traditional HWE use in the corporate, retail, hospitality and other environments up to 95%, if not eliminating it all together (excluding specialty spotting and stain removal where needed). I can’t even express what a game changer this system is! Infinite Floorcare currently employs 3 Fast Foamers and I can honestly say in the 3 1/2 years since using and mastering the equipment, we haven’t taken a traditional box extractor and wand on any of our maintenance or restoration jobs more than a handful of times, and those have typically been restaurants.
Steve Brown, Infinite Floorcare
Four 10 Hour Shifts
Now I understand that some states have labor laws and I will go ahead and apologize to you for even bringing this up, but if you aren’t doing this already, you absolutely need to explore this option because not only will it make you more efficient and profitable. Every technician out there would love to have three days off a week. Here’s a quick breakdown of how and why it’s so beneficial:
In an 8 Hour Work Shift:
- 1 hour of drive time
- 30 minutes lunch
- Two 15 minute breaks
- 6 hours of onsite labor (2 hours non-production of a 8 hour shift)
- An average technician can low moisture clean 1,200 sf per hour (without the Fast Foamer) = 7,200 sf/shift
- An average technician can extract 600 sf per hour = 3,600 sf/shift
- 3,600 sf @ .18/sf for extraction is $648/day
- 7,200 sf @ .08/sf for low moisture is $576/day
In a 10 Hour Work Shift:
With the same drive time and breaks as the 8 hour shift:
- An average technician can low moisture clean 1,200 sf per hour (without the Fast Foamer) = 9,600 sf/shift
- An average technician can extract 600 sf per hour = 4,800 sf/shift
- 4,800 sf @ .18/sf for extraction is $864/day
- 9,600 sf @ .08/sf for low moisture is $768/day
When you have a four 10 hour shift, you free up equipment by 20% allowing 1 more day a week for someone else to use it. If you look at a 10 hour shift compared to an 8 hour shift and look at actual hours worked, it’s more efficient. Eliminating drive time, breaks, and lunch, technicians are only 75% productive on an 8 hour shift (6 ÷ 8) vs. 80% productivity for a 10 hour shift (8 ÷ 10). Techs like it too because it’s 1 less day to drive into work, fewer miles on their personal car (plus the cost of gas), and it’s like having a holiday every week.
Bob Deweese, Rite Rug
Hard Surface Wand with Extractor for Resilient/Hard Floor Care
I know I sound like a broken record, but when you can rinse the floor with water pressure (sorry walk behind equipment) and vacuum the slurry up in a single process, what are you waiting for? Oh and by the way, that slurry is contained in a vessel that will not slosh around and spill while transporting it back to the janitorial closet to dump like every known bucket and mop system out there (full disclosure, I have cleaned up after myself too many times while transporting the bucket and hitting a transition strip). As the old saying goes, “But wait, there’s more.” Let’s talk for just a minute about the quality of rinsing on materials like bonded rubber crumb flooring or the fact that with the vacuuming of the rinse water your floor will be ready for either finishing or putting back into service that much quicker.
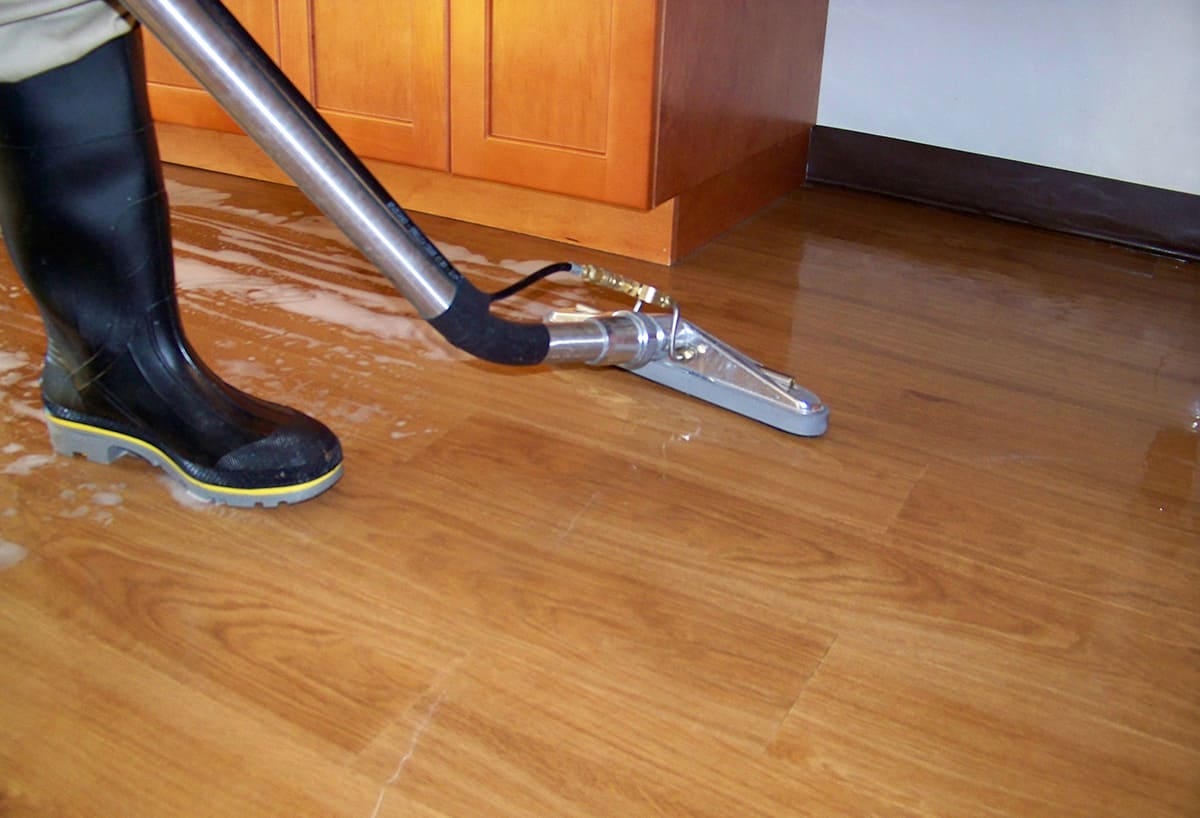
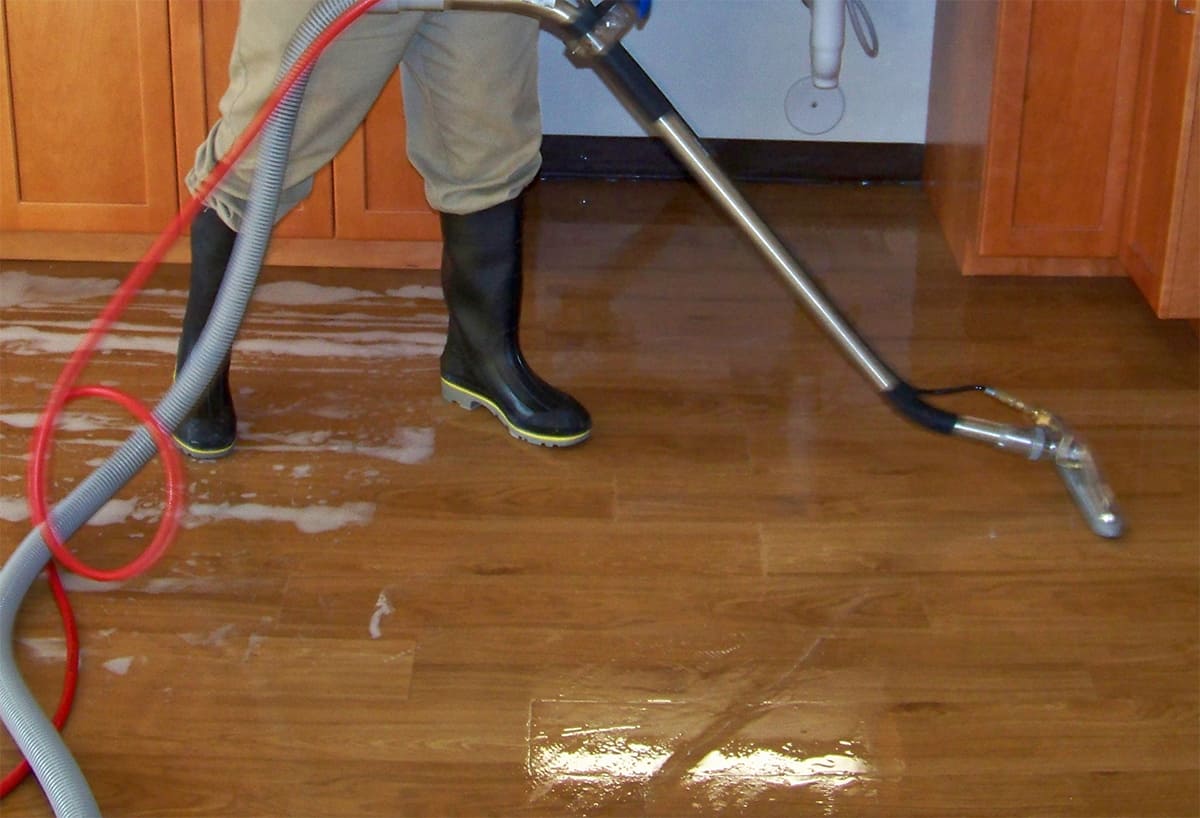
For us, the ability to remove slurry and rinse the surface at the same time exponentially increases our productivity! Beyond that increase, we have taken out of the equation the opportunity for accidental spills of slurry water between the project area and the disposal of the water. What I mean by that is, there’s no longer an issue with the technician rolling a mop bucket and hitting a transition between two surfaces and splashing dirty water everywhere.
Bob Deweese, Rite Rug
Malish Mal-Grit Lite Brush for Textured Resilient
A constant question I receive is, “How do I get the texture surface any cleaner?” My answer is STOP USING A PAD! The definition of insanity is doing the same thing over and over and expecting different results. Well, if the shoe fits. This brush by Malish (Mal-grit Lite) is the perfect denier for getting into the ticking on LVT or down deep into bonded rubber crumb flooring.
It makes too much sense to use a brush in your everyday cleaning. On textured flooring (especially rubber) a pad just cannot get down into the valleys of the flooring. Using these brushes will end up saving time, money, and frustration.
Spencer Luallen, MilliCare Floor & Textile Care
Training (Because Call Backs Kill Profit and Productivity)
Now I’m sure I sound like a broken record so I will make this short and sweet. An average IICRC CCMT or RFMT class might cost you $350, but a call back to go and do a cleaning due to any number of issues can cost you that (or more!) in just one trip. Add up how many call backs a year your company has and then ask if any of those might not have happened if the technician was better educated.
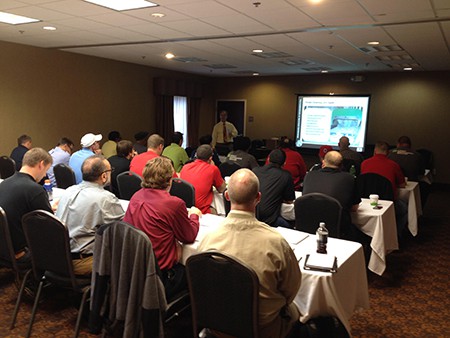
Call backs are a direct reduction in profitability and create added stress for managers and salesman. Technicians don’t want them either so they are almost always receptive to any additional training that can be provided. Besides improving a tech’s physical skills and providing him/her with applicable knowledge, training also builds confidence which is a necessary key ingredient in solving problems in the field or making a correct, informed decision in the field to avoid a call back.
Steve Starcher, MilliCare Floor & Textile Care